Aerospace technology
Zero-error tolerance also applies on the ground
For everything to do with aerospace technology, there is an unspoken zero-defect tolerance. This golden rule applies not only in the air, but also on the ground - for all trades involved in aerospace technology. The relocation company HARDER logistics is familiar with the strict requirements from numerous projects.
- 1. Experienced in documentation
This is why our own staff, who we train individually for deployment in the division, leave nothing to chance. The deployed employees are familiar with the high documentation requirements. Everything that is moved can be tracked transparently. We also clearly regulate which of our employees are authorised to move around the site in the relevant areas prior to deployment. To this end, we work with the customer to define which access regulations are required and ensure that the names of our employees are filed with the plant management.
Report about Diehl Aviation
What does a project for aerospace technology look like in concrete terms?
- 1. the example project
The aircraft supplier Diehl Aviation has set up a new production plant for aircraft interiors in Hamburg and bundled its previous locations in the Hanseatic city. The associated relocation logistics took a year, from the initial planning to the transport of the last box.
- 2. The key data
Almost 300 workstations were relocated, 8,500 m² of space was restored to its original state and a total of 40 lorry loads were transported, including a milling machine over 10 m long.
- 3. Relocation in two stages
After the preliminary planning, which lasted around six months, the first partial relocation took place. The actual relocation involved 150 workstations. In addition, HARDER logistics took over the maintenance of the machines as well as their professional dismantling and assembly. Once the hall had been cleared out, the HARDER logistics team restored the 5,000 m² area to its original state and handed it over swept clean. This also included the disposal of old machines, the moving of walls and the removal of shelving systems and paternosters. The second part of the move involved 120 workstations and the closure of the 3,500 m² site.
- 4. The challenge
Part of the removal goods was a milling machine measuring 10.20 metres long x 4 metres wide. In order to be able to load it, it was first dismantled to its transport dimensions of 3.50 metres. The preparatory measures alone took three days and included the creation of cable assignment plans and interface photo documentation. A low loader transported the project load to the new location.
- 5. Team and equipment
A total of eleven employees from the Neu-Ulm logistics service provider were on site during the project period, including electricians and mechanical engineers. The company's own equipment consisted of three vehicles with customised superstructures specially designed for relocation projects.
- 6. The conclusion
The well-planned stages of the move meant that production was affected as little as possible. Sufficient pre-production, the co-operation of all those involved and a good process contributed to the fact that the business partners hardly noticed the effort involved.
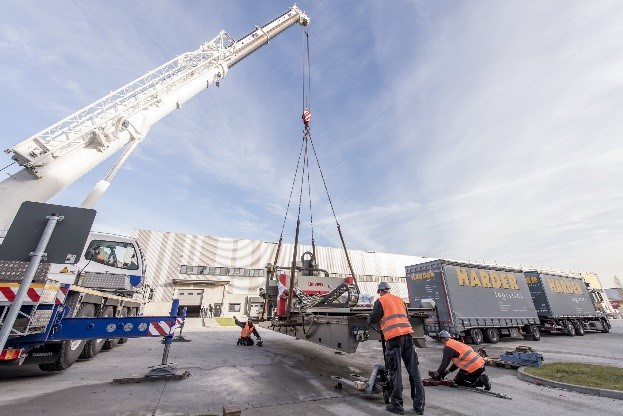
The moment of setting down the milling machine requires the highest concentration. The 70-t crane lowers the 10-metre-long project cargo millimetre by millimetre.
It took around three hours for the milling machine to be properly installed in the leakage pan at its new location on Genter Ufer.
Photos: HARDER logistics / C. Brinkmann